After all, a car has two armchairs in the front and a sofa in the back, all made with a metal skeleton with seat and back surfaces in Pullmaflex, a kind of metal mesh that can be tensioned to varying degrees for comfort. The good thing was that the wires could be stretched to provide lumbar support, unlike normal canvas which is non-stretch and therefore uncomfortable.
A flexible failure
Inspiration on wheels
IKEA has always tried to find new, smarter ways of packing and distributing furniture. At the end of the 1970s, IKEA took inspiration from car seating in its attempts to pack sofas and armchairs into flat packs.
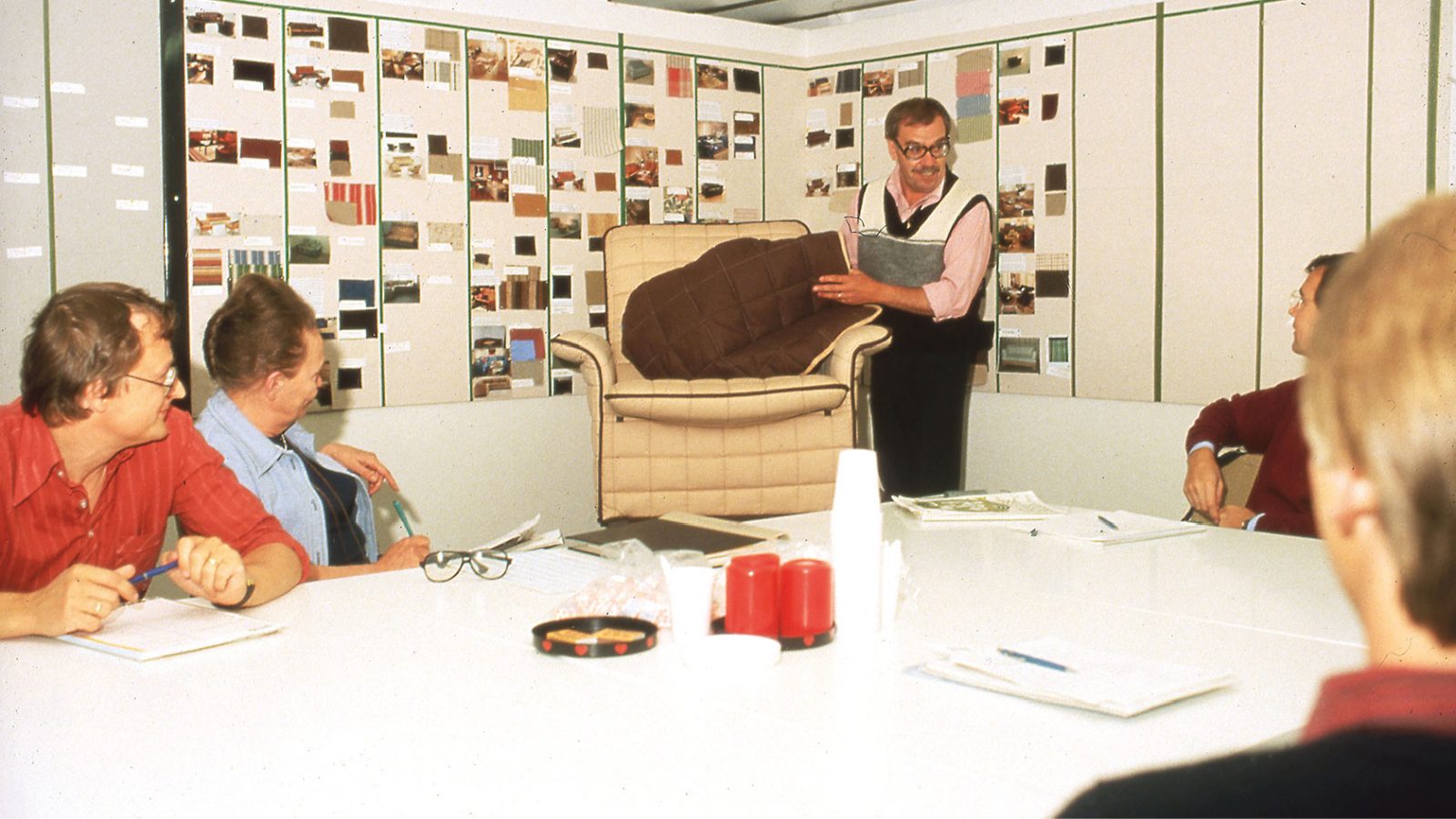
The original idea came from Danish designer Niels Gammelgaard, who began looking at Volvo car seats. On several occasions, product developers at IKEA and Volvo Cars got together to exchange thoughts and ideas. Lars-Ivar Holmqvist, a buyer at IKEA at the time, remembers how the discussions went. “IKEA thought that if the car industry could make upholstered metal skeletons for not much money, surely we could do something similar.”
Right there and then, there was great enthusiasm for the idea. The company MITAB in Tranås was asked to manufacture the steel frame. For comfort, the same kind of material used in car seats was used: Pullmaflex, the flexible material that provided lumbar support. The TULLANÄS series was born. “But the frame wasn’t the problem. The problem was with the covers,” Lars-Ivar Holmqvist explains.
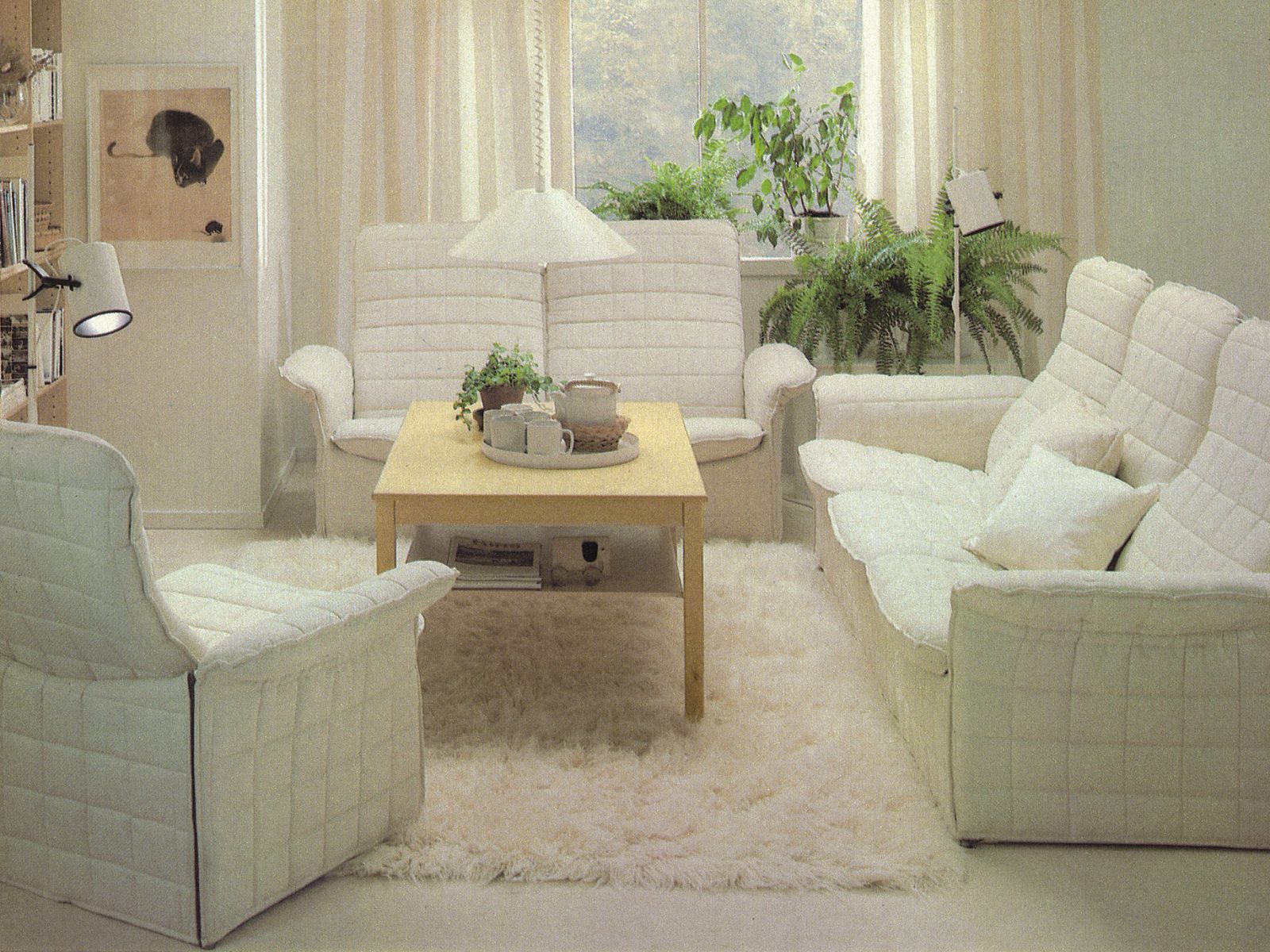
Korean textiles
The armchair and sofa covers would be made by the clothing industry in South Korea, which Ingvar Kamprad had recently visited. Apparently, he told co-workers that IKEA would have the TULLANÄS covers made by the Korean clothing industry, because “…they’re really good at making winter coats and shirts and clothes in Korea.” The fabric would be made with quite a complicated method that was used in Korea at the time, whereby different coloured pieces were joined and dyed to achieve the same shade.
IKEA normally maintains close contact with its suppliers and visits the factory often, especially for new products. But this was not easy in the 1970s, when the trip from Sweden to the factories in rural South Korea took several days by air and rail.
“We couldn’t keep going there all the time to keep an eye on the process,” says one of the purchasing managers at the time, Svante Smedmark – one of the few people who were sent there ahead of production. He feels that a few more visits would have been a good idea, because covers of this kind require absolute precision. If they are not perfect to the millimetre, the finished cover is either too loose, or too tight and can’t be pulled on. “The car industry was good at cutting fabrics very precisely. But IKEA wasn’t, especially from so far away.”
“That’s not enough,
let’s order 40,000.”
Impossible instructions
Everyone involved in the TULLANÄS series had complete faith in it. When 10,000 sofa covers were ordered, Ingvar thought that wasn’t enough. “No, let’s have 20,000,” he said. Then someone else felt that, “That’s not enough, let’s order 40,000.”
The steel skeletons, which were made in Sweden, were ready in plenty of time. And while waiting for delivery of the sofa and chair covers from South Korea, TULLANÄS was promoted with beautiful pictures in the catalogue in the early 1980s. But when the tens of thousands of quilted cotton covers finally arrived, they were so varied in colour that the TULLANÄS sofas and armchairs couldn’t be sold. And several of them were extremely hard to pull onto the steel frames. “The problem was that everything had to be done in a blind rush, which sometimes happened when Ingvar was involved,” explains Svante Smedmark.
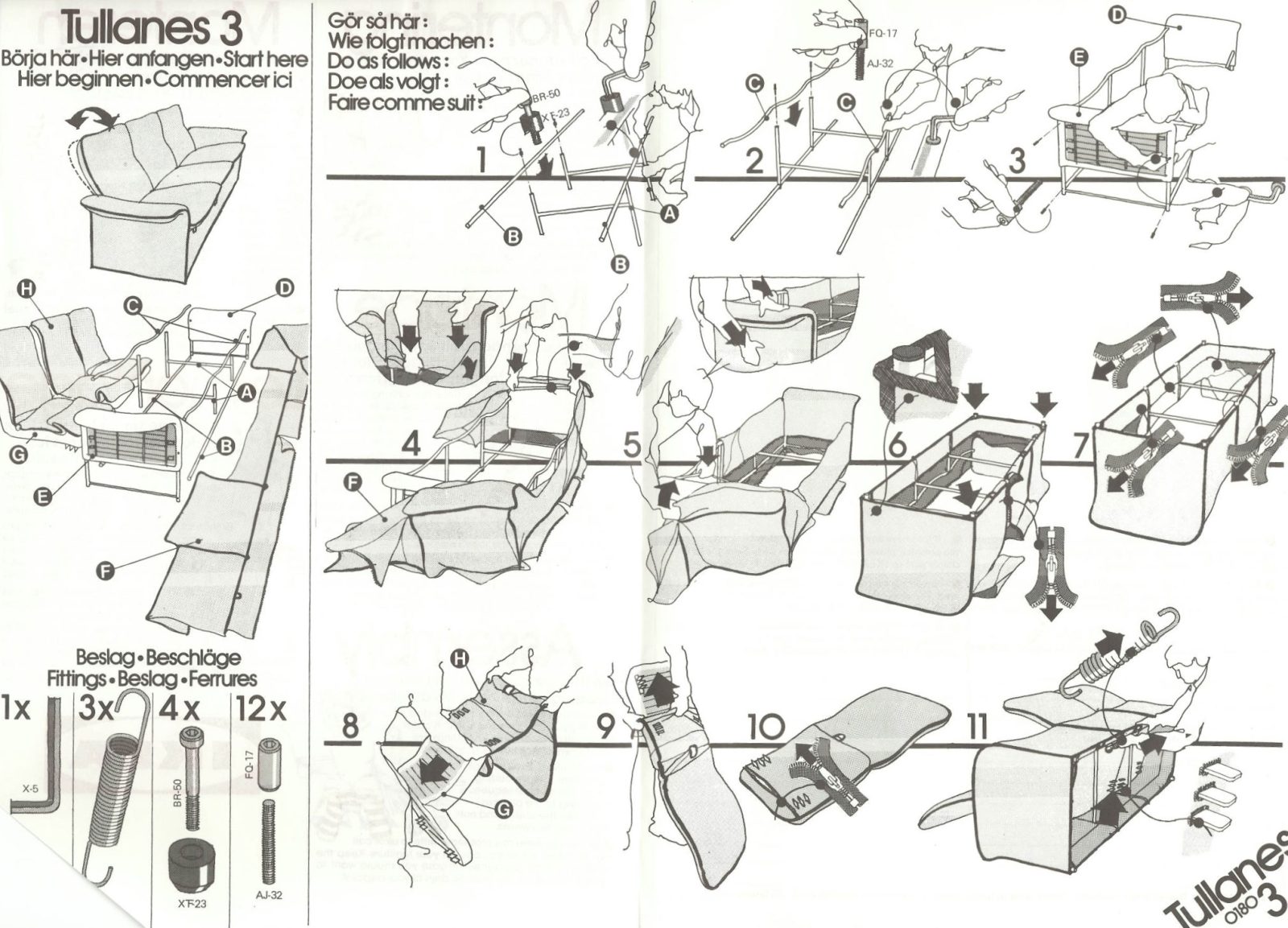
Occasionally, an idea is better than the end result. Throughout its history, IKEA has always experimented extensively, and several failures have sometimes been needed before a solution is found. Some projects were abandoned before the products reached customers, while others were discontinued or were very short-lived, such as TULLANÄS. But even when things are going a bit wrong, there are valuable lessons to be learned.
Designer Niels Gammelgaard could not let go of the idea of making metal chair frames. He was inspired by design engineers in the car industry, and visited a factory that made shopping trolleys out of steel wire, bolts and flat iron bars. This led to the creation of MOMENT, the world’s first sofa that could go into a flat pack.