Innovation in the world of textile began in earnest at IKEA back in the mid-1960s. To begin with, the main focus was on quality testing, and on bringing more colour and modern patterns into Swedish homes, which were quite grey at the time. At the new IKEA lab in Älmhult, IKEA textile engineer Börje Lång tested thousands of natural and synthetic fibres to find the best fabrics for furniture, curtains and blankets. In the 1964 catalogue, IKEA proudly talks about equipment that “relentlessly reveals abrasion resistance, machines that test light fastness, resistance to friction and material composition”.
Tomorrow’s textile
Innovation through the ages.
Textile, after wood, is the most extensively used material at IKEA through the ages. It appears in everything from bed linen to curtains, and increasingly incorporates smart functions like dampening sound or absorbing heat. It’s impossible to imagine a world without textiles. And that’s why, for a long time, there has been intensive development of innovative production techniques with less impact on the Earth’s resources, while also making the most of textile’s potential beyond its soft, cosy and aesthetic qualities.
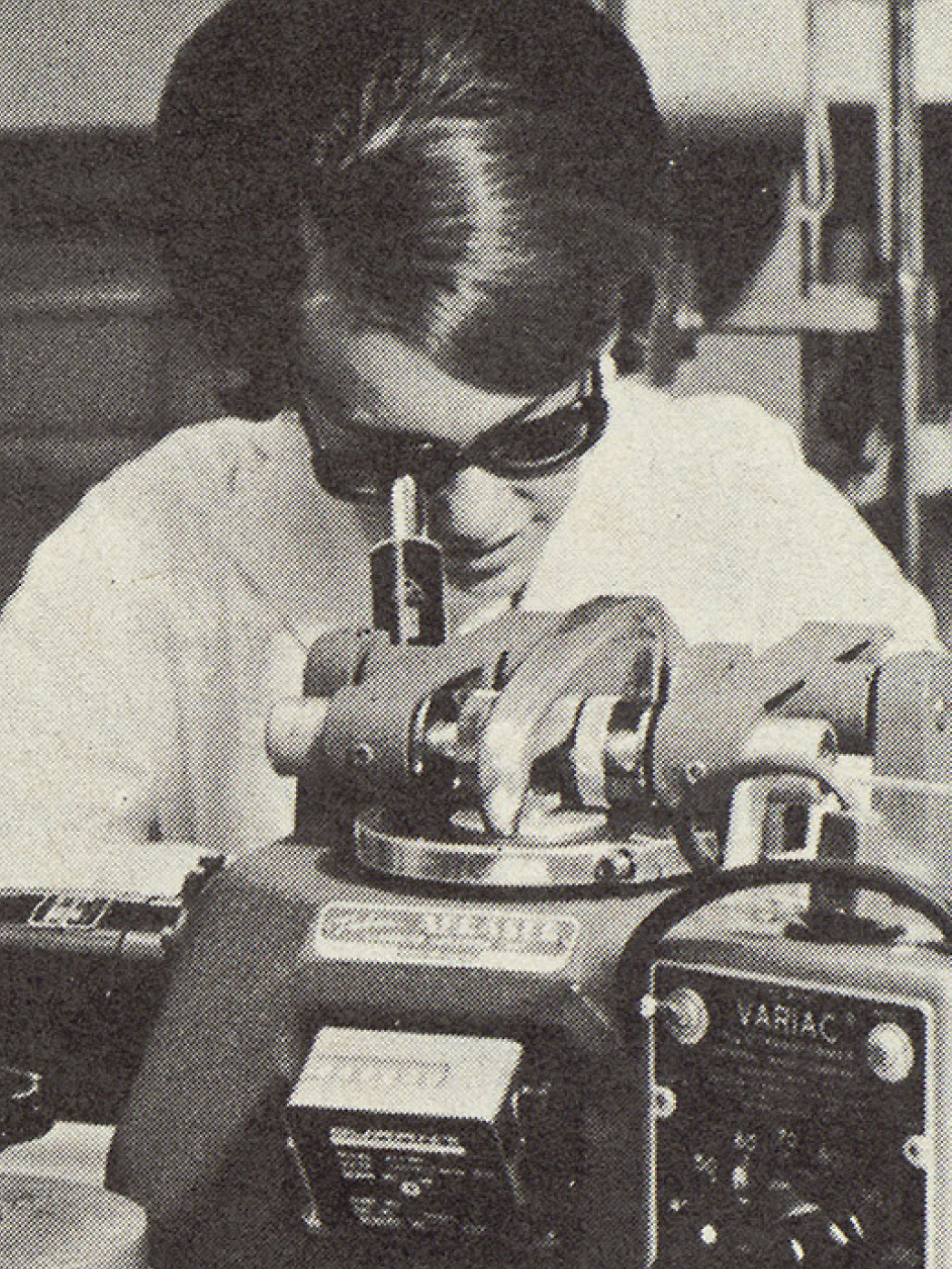
In the lab – which IKEA claimed was the first in Sweden to be run by an independent company – the idea was to be able to discover early on the options that offered the best balance of quality and low price. In the 1970s, the curiosity and inventiveness of the IKEA textile department not only led to some groundbreaking design, but also to new weaving techniques and experiments with different natural fibres and furniture upholstery in unexpected materials.
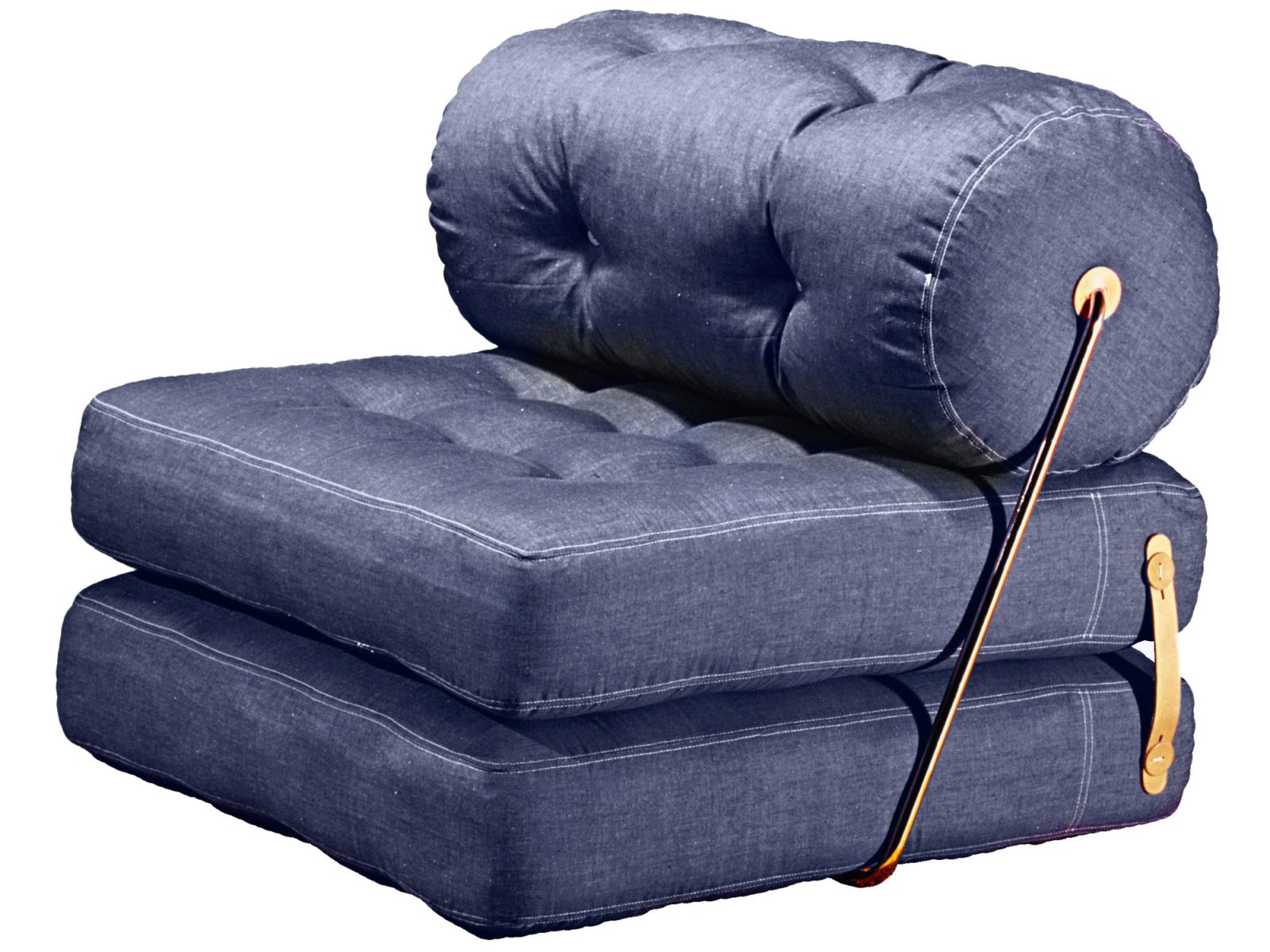
The textiles of tomorrow
The new millennium brought higher demands for clever functions and durability, particularly from an environmental perspective. This was when ideas were born about products like sound-absorbing curtains, and sofas that could change patterns depending on the ambience in a room. And in the 2010s, work in the IKEA innovation labs intensified even further. Also on the agenda was improving the technology for recycling and reuse, which takes place in close collaboration with universities, research institutions, organisations and other companies. The long-term goal for IKEA was not just to benefit its own business, but to be a part of driving positive global development in the entire sphere of textiles. In 2016, this ambition attracted Linda Worbin – at the time a professor of textile design at the Swedish School of Textiles in Borås – to IKEA. She was ready for something new, and wanted to speed up the development of smarter, more sustainable textiles.
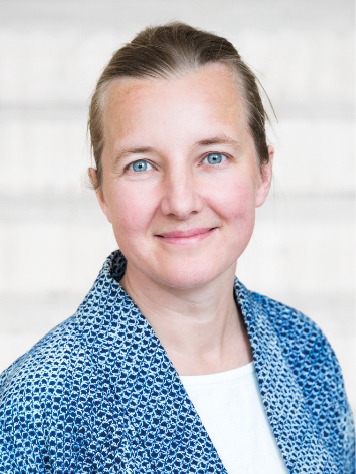
“I couldn’t see any other company that could do this on the same level as IKEA,” says Linda, who today works as a material and innovation developer at IKEA. “It’s not just about developing smart materials, but equally about choosing meaningful ways to use them. Our team is tasked with working with innovation in the long term. And of course we can’t do that alone; we work with many other players, as well as with our customers.”
Heat development
We find Linda Worbin at one of the long tables at MUMS, the huge, buzzing hall for fika breaks and meetings for people working in product development and future home furnishing at IKEA of Sweden in Älmhult. Beside her is Carmen Stoicescu, product design engineer in a product development team that has produced several temporary innovative IKEA collections, and continuously tests new ideas. Between them on the table is a grey-and-green-striped oven glove – one of the results of several years of research and product development.
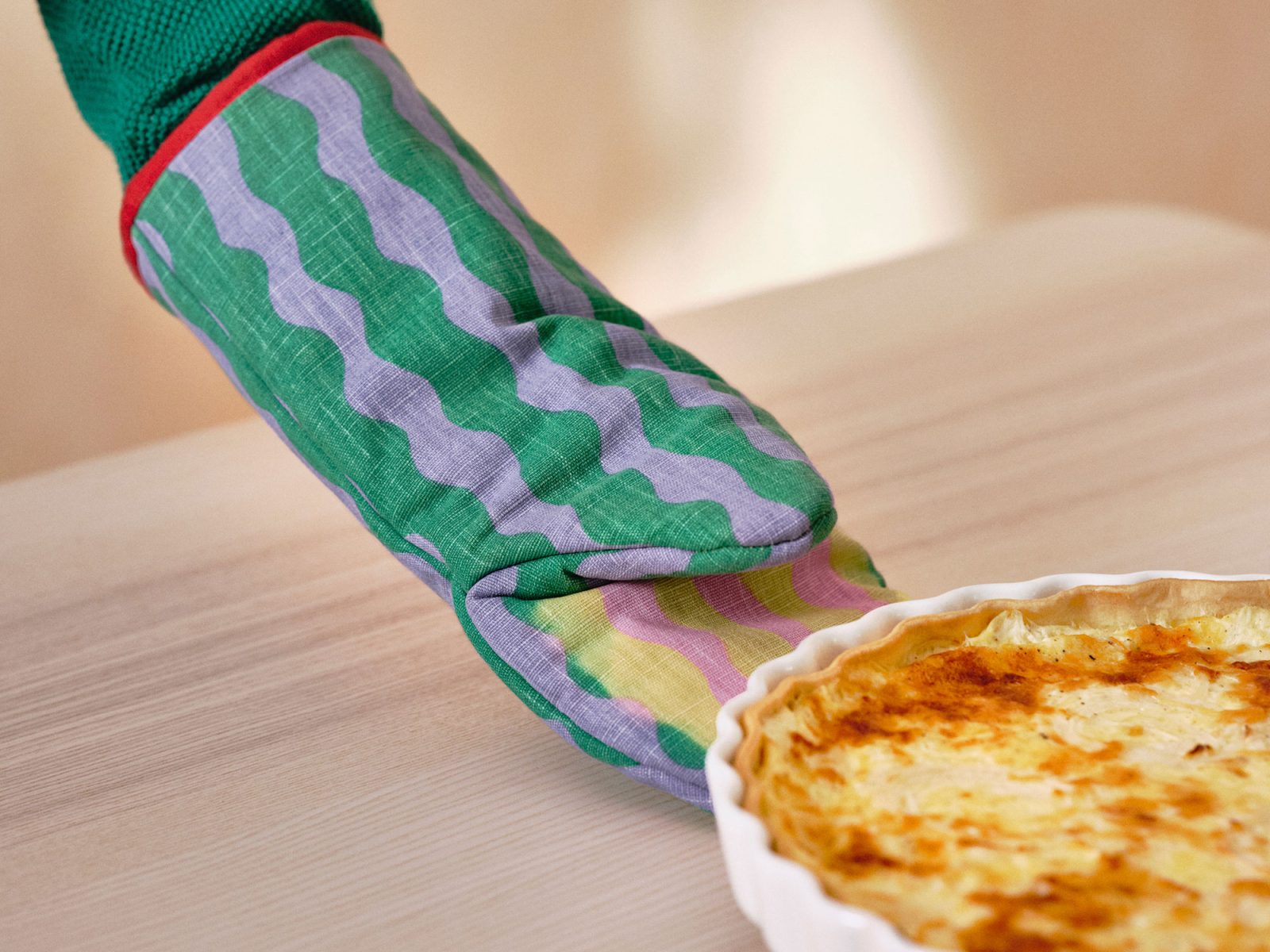
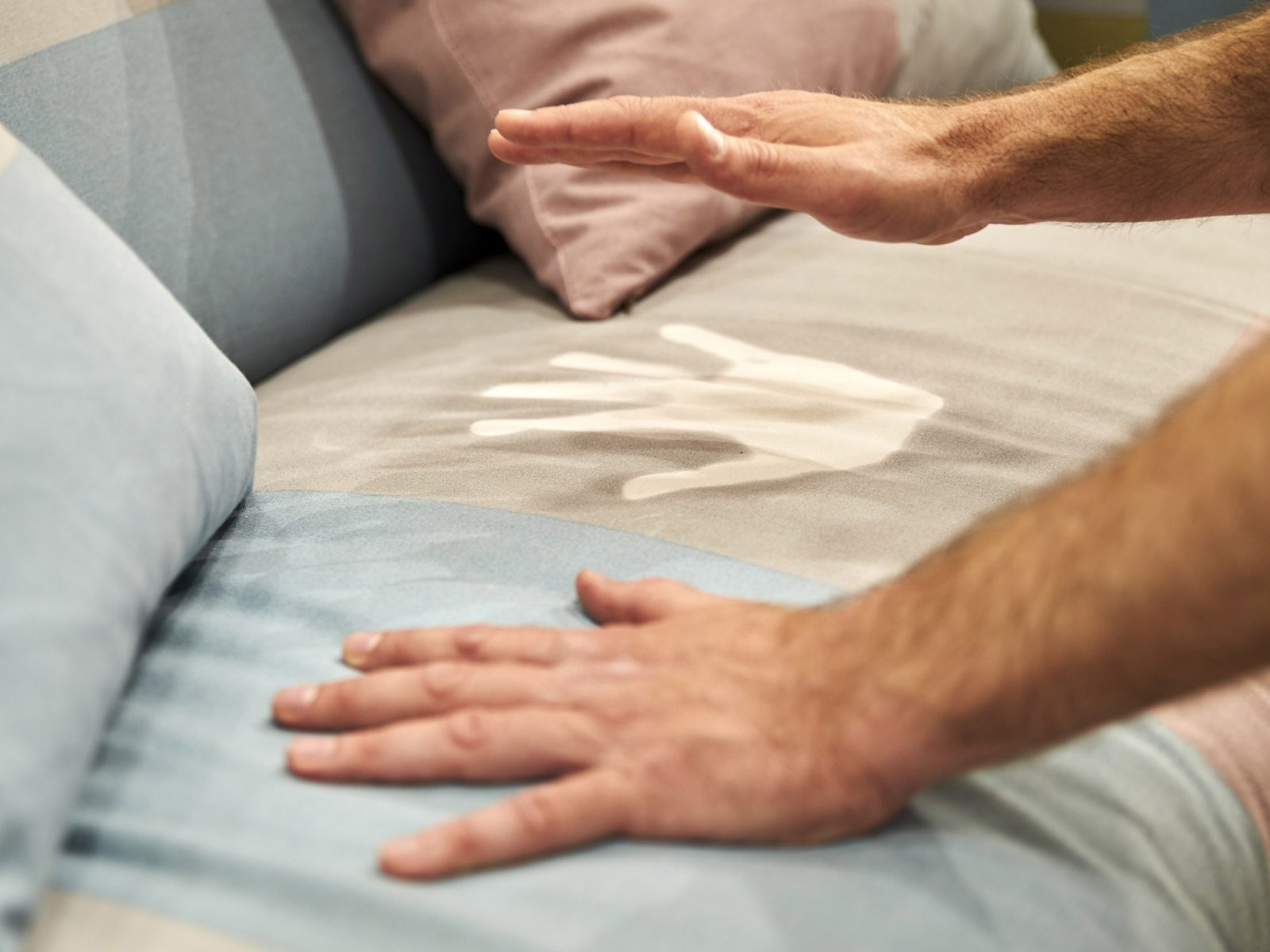
Carmen has just put a glass jug of hot water on the table. She puts on the oven glove and grips the hot jug firmly. As if by magic, the grey-green quilted fabric starts to change colour. “The oven glove is one of several kitchen products for families with children, where innovative technology is used,” she says, letting go of the jug and showing how the glove gradually returns to its original colour. Together with Linda and her innovation group, Carmen’s team has spent a couple of years studying heat-sensitive colour pigments that can make fabric change colour and expression based on temperature.
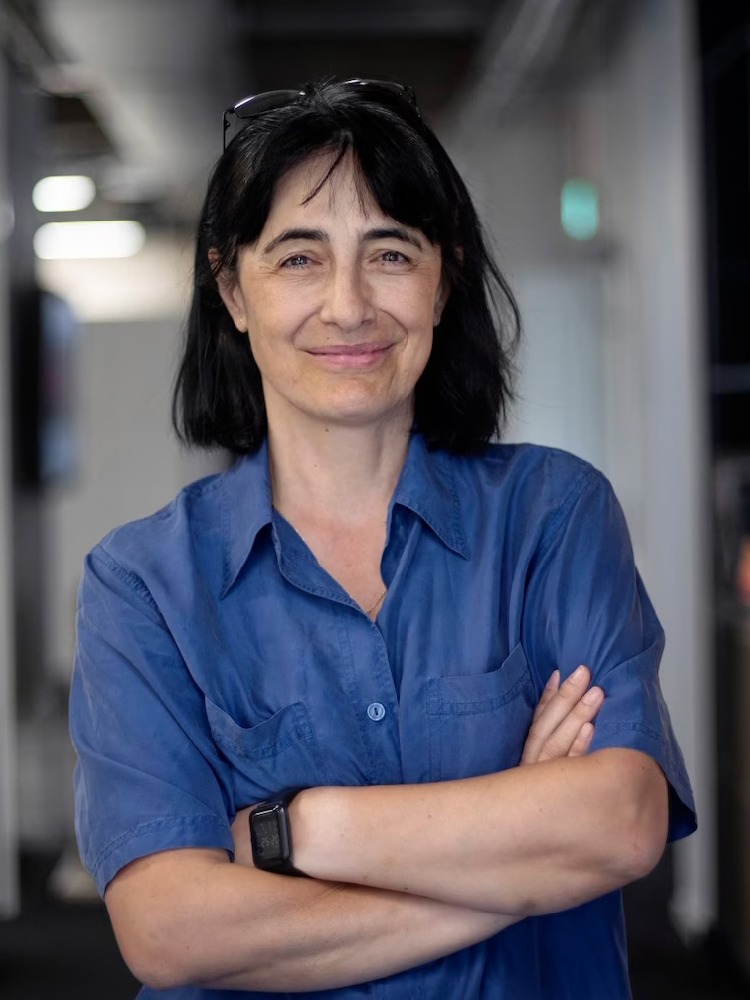
“It was important that the function wasn’t just a fun thing, but also useful,” explains Carmen, and Linda nods in agreement. “The oven glove is an example of how IKEA takes an existing function – heat-sensitive colours – and takes a new approach to how they can be used in our homes. Like in the oven glove, which shows how hot an oven tray or saucepan is,” says Linda. Her team began experimenting with heat-sensitive colour powders back in 2017 to develop ‘recipes’ – exact blends of different pigments – in order to achieve different expressions and functions. After that a series of safety and quality tests followed before the next challenge: finding meaningful ways to apply the functions to make everyday life at home a little better.
“Once a collection like this is finished, we can try out the new technology, our thoughts and ideas, on a global level and on different markets,” Carmen explains. “We then get a lot of feedback from customers, which helps us to evolve so the next product can be even better.”
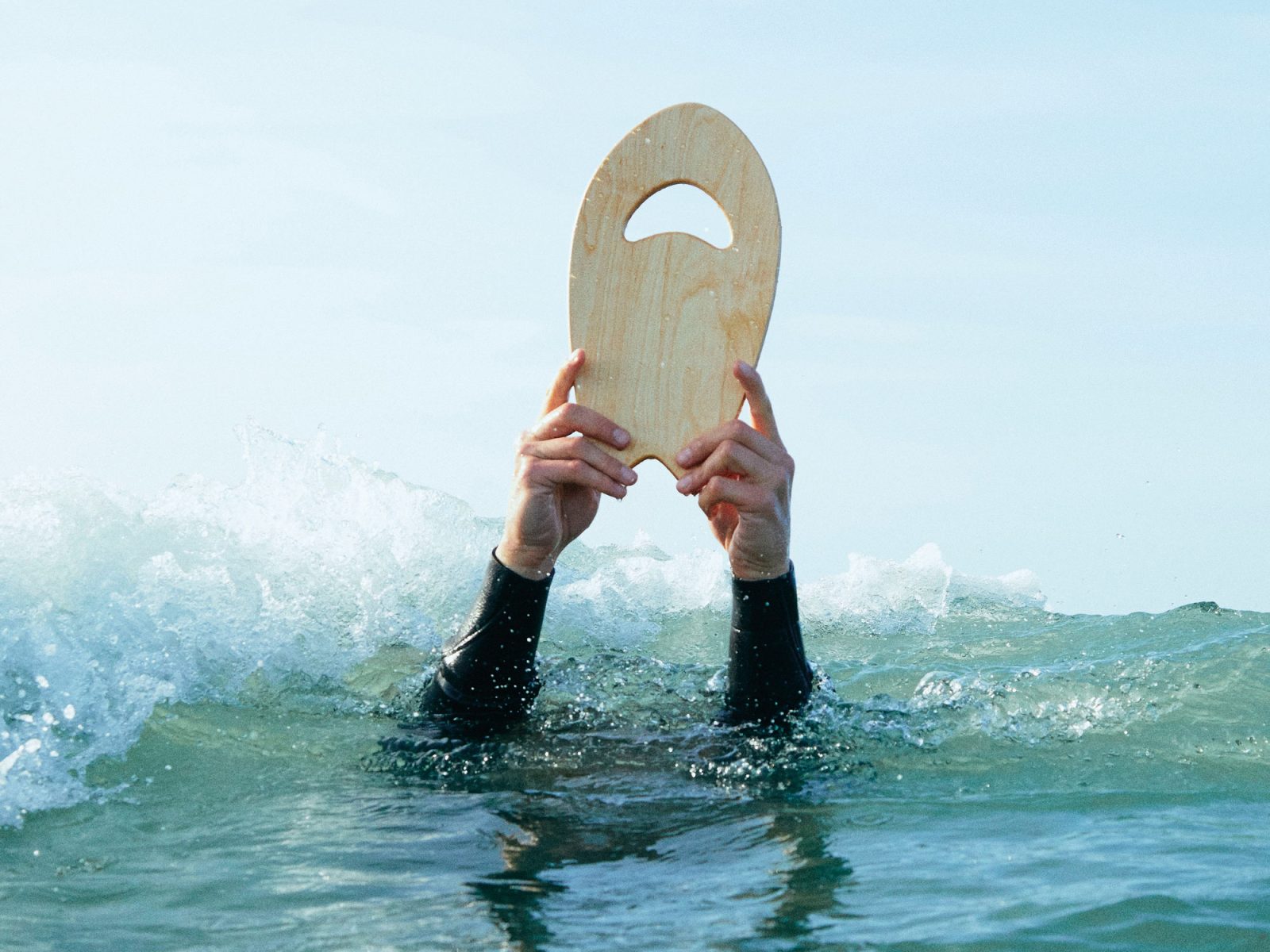
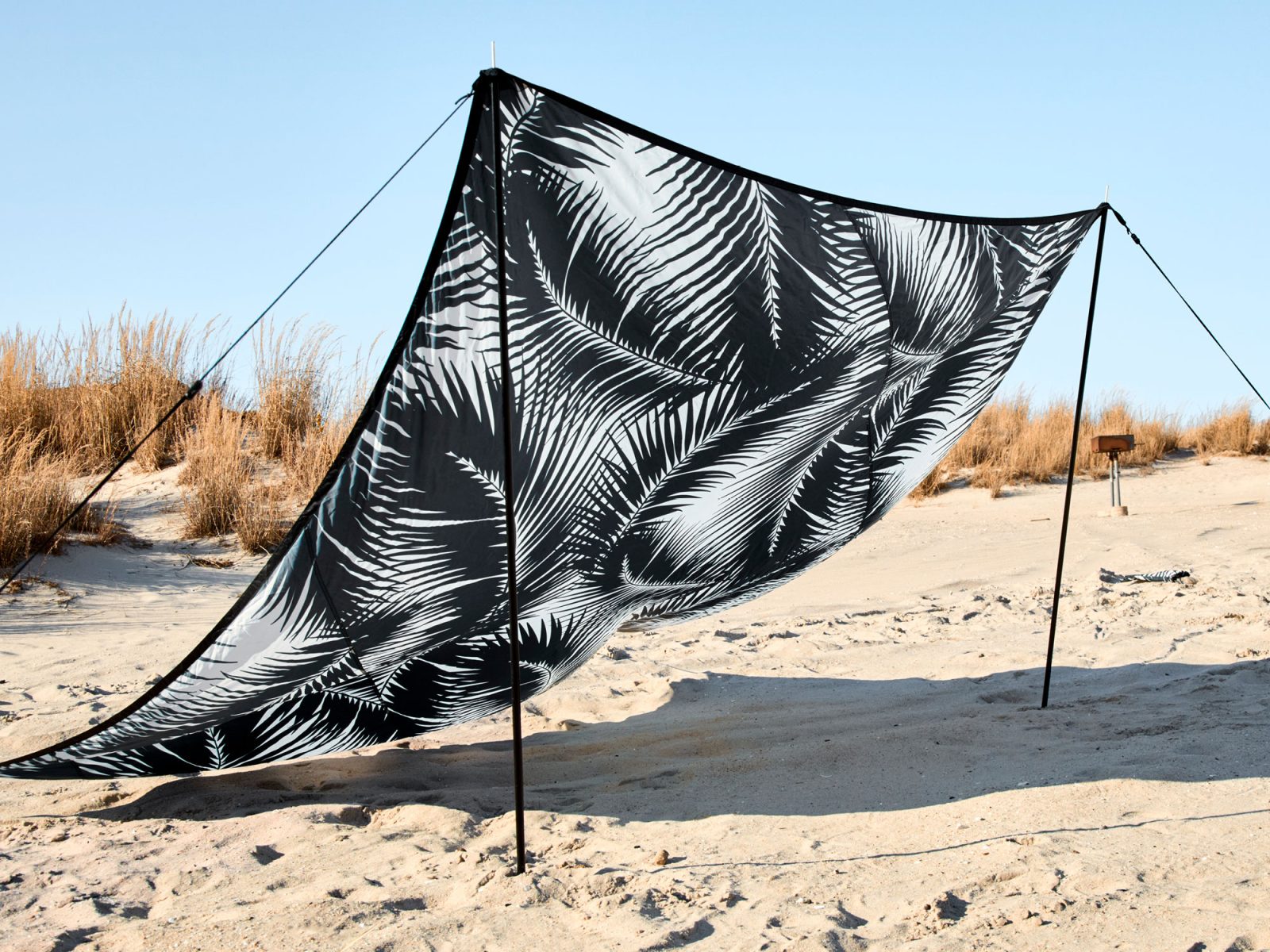
Clever and sustainable
IKEA has an ambition for 2030 to only use recycled and renewable material in everything it makes. Fossil raw materials like virgin polyester will be replaced by bio-based alternatives or recycled material. So far IKEA has mainly worked with land-based raw materials, but for the past four years Linda and her colleagues have been experimenting with marine materials, for example. Is it possible to make sofa covers and duvet covers from seaweed?
“We’re looking at what it might entail for the environment, and whether using marine materials can meet our requirements in terms of large volumes and the ability to scale up. You must look at the entire value chain, from what kind of tools go into the sea, to how raw material can be transported and handled,” says Linda. “The process is still in its early days, and it may of course turn out to be impossible. If so we’ll move onto something else, but we’ve still learnt a lot in the process. It’s great to have the resources to be able to work proactively. IKEA is not an established research institution, but we’ve always been driven by curiosity. Our brand also has deep respect for knowledge, and a tradition of refining and improving on existing technology. But the age we live in also places demands on brand new solutions and raw materials – as the world needs to reduce its carbon dioxide emissions.”
Not static
In the old days in Sweden, fabrics like linen and wool were woven and cared for to last at least a lifetime, and were made to keep their properties and functions over their entire life. Linda Worbin believes that a major shift is now under way, to enable textiles to have several functions – and even change functions – across their life span. Like the conventional oven glove, that can also visualise temperature. “By using interactive materials, we can create both multifunctionality and individual customisation,” Linda explains. “Not everyone wants the same kind of comfort, for instance. Some like to change things around in their home often, so it’s good if they can change the products they already have, rather than having to buy new ones.”
“IKEA has become very good at choosing the right material for the right application. Now we also need to think about how the materials can last longer by enabling more applications later on in their lifetimes. In the future, many textile materials will be developed to interact with their surroundings and change with time. Designers and product developers can no longer see textile as a static material, but rather something that goes on evolving with time, based on different situations.”
Eco-thinking for the modern age
In a world of limited resources, IKEA collaborates with others to find new ways of doing more with less. According to the UN Environment Programme, the textile industry is responsible for more of the world’s carbon dioxide emissions than international shipping and aviation put together. If nothing is done, this could lead to a 50% increase in emissions by 2030. If IKEA is to increase its share of recycled textile materials in production, a new way of thinking is needed at all levels.
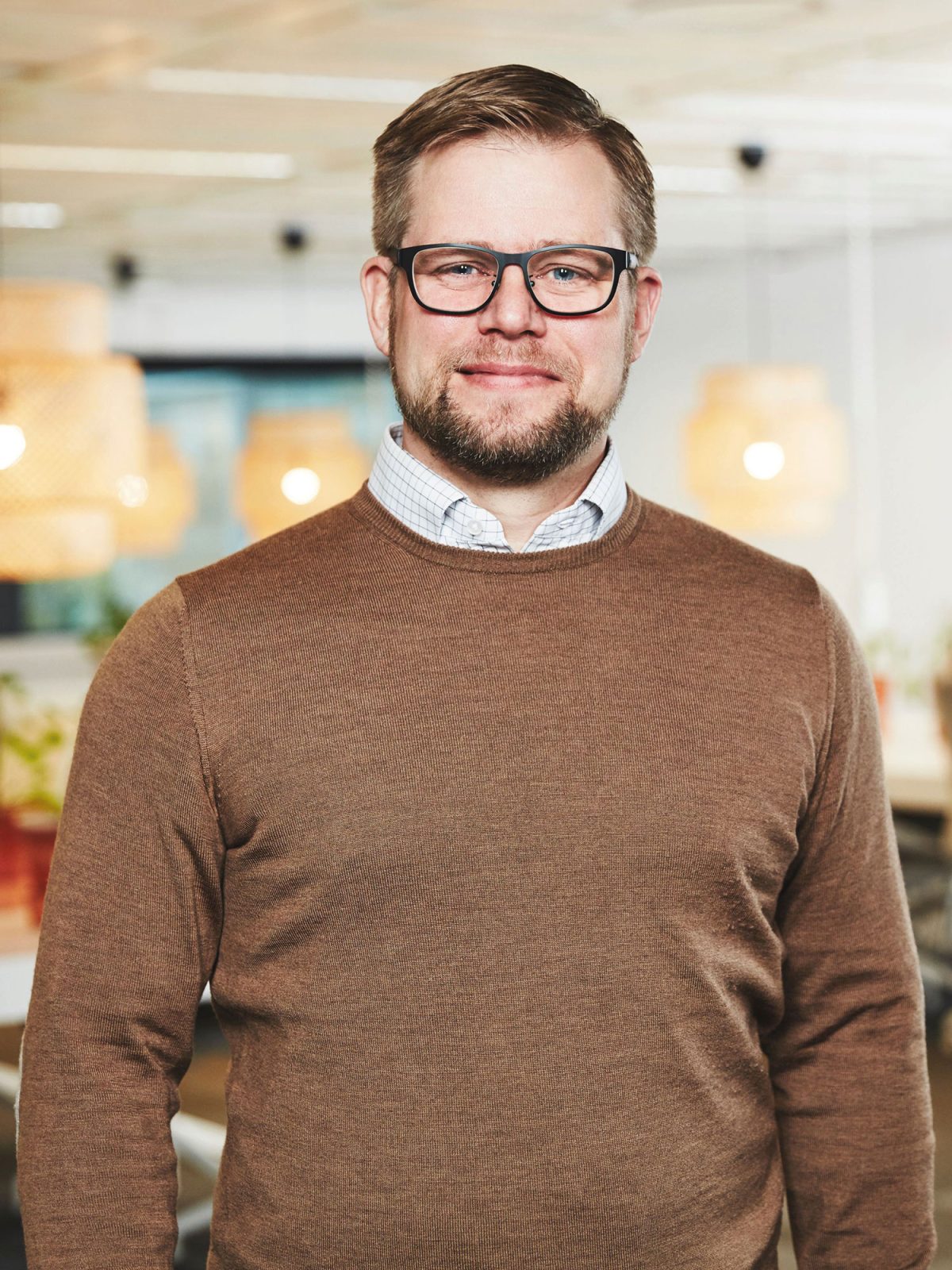
“Discussions about textile and sustainability began already back in the 1980s, but the journey towards real change started at the turn of the millennium,” says Nils Månsson, category manager for textile at IKEA. That was when the decision was made to start replacing oil-based materials like polyester and polypropylene with recycled polyester. This placed some tough demands on technical development of the processes for both recycling and reuse. Already by 2020, 90% of all the polyester used at IKEA was recycled polyester. But a lot remains to be done.
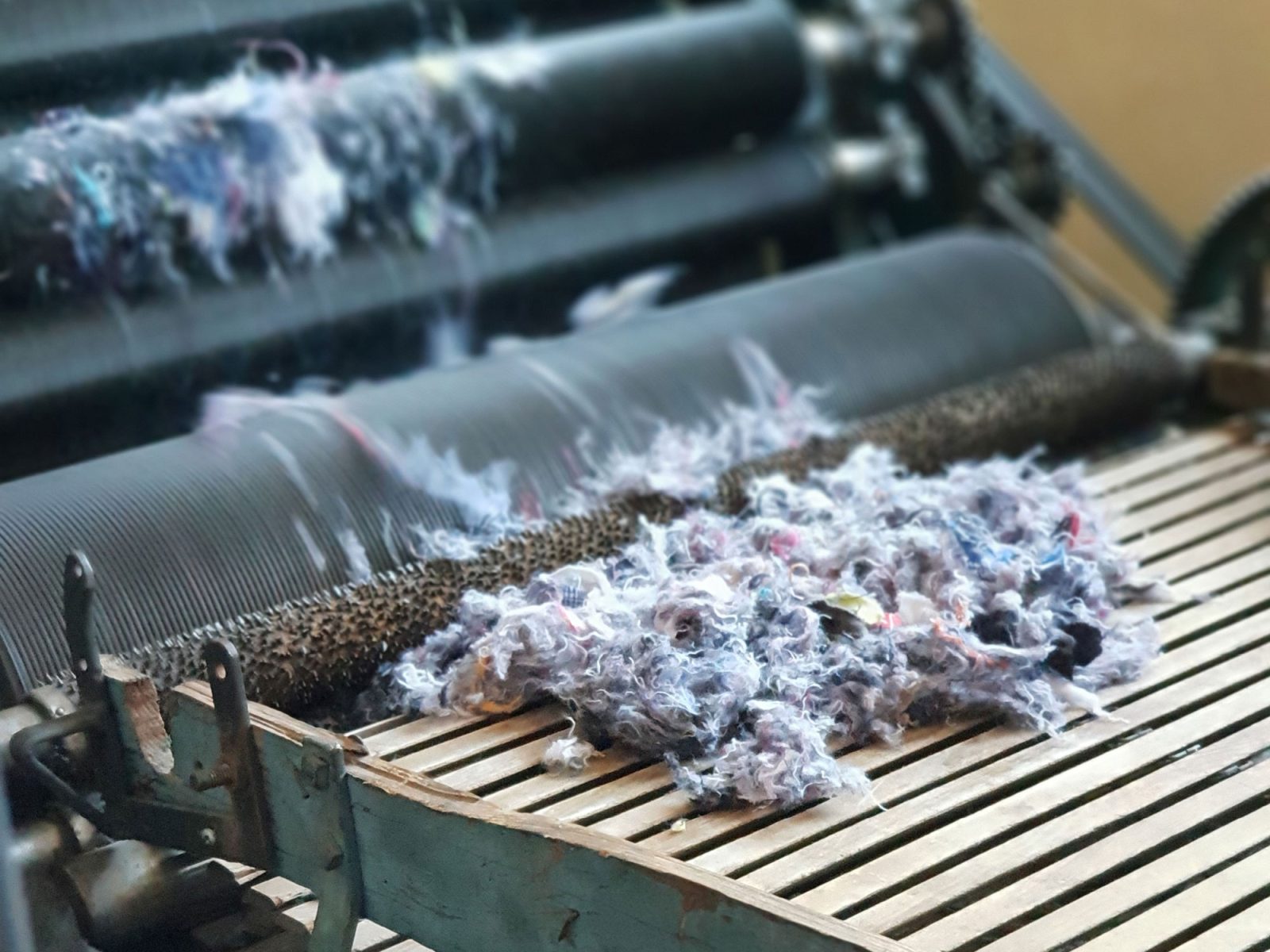
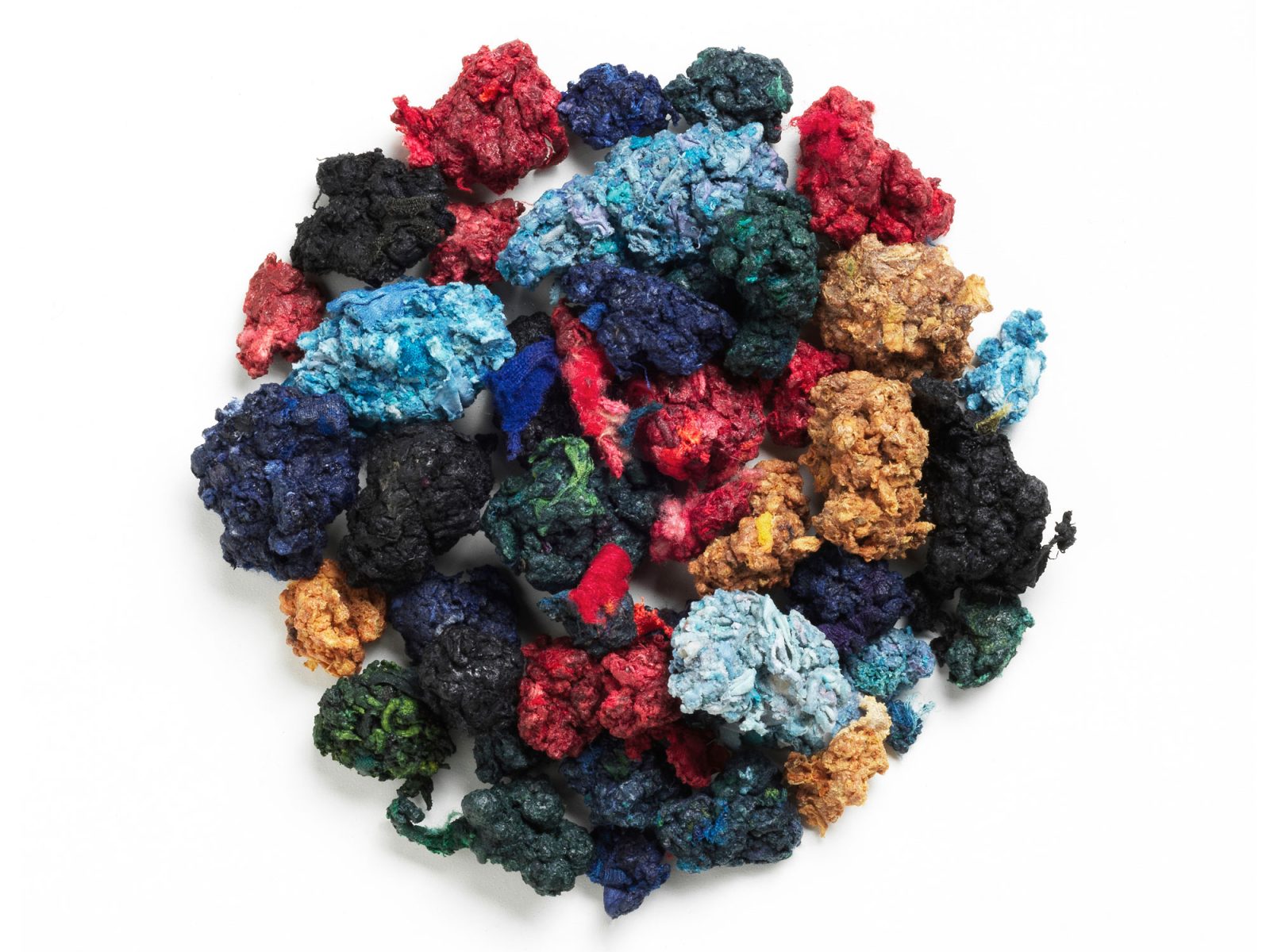
“We make progress and get a little better every day. Meanwhile, big changes are under way when it comes to water use and energy in textile production – dyeing cotton, for example, uses a lot of hot water. We want our suppliers to use renewable energy sources, solar or bio-based, and also need to make sure that no chemicals are released into the environment. In this, IKEA has far stricter requirements than most countries,” says Nils Månsson.
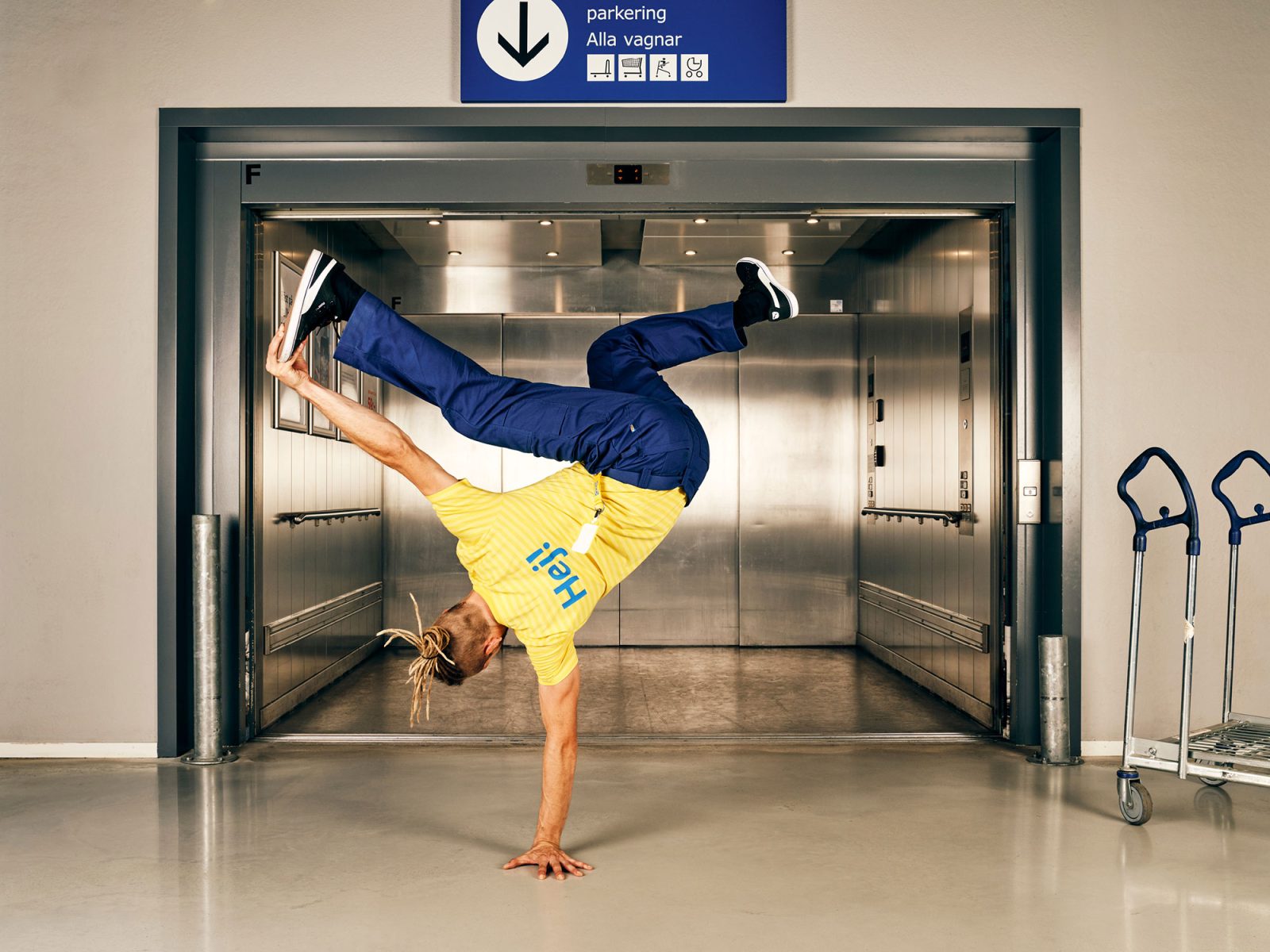
IKEA wants to be a part of driving developments globally, and we work with everyone from local cotton farmers to UN organisations and other large companies, but things need to speed up, according to Nils Månsson. “The world population is growing, but there’s a limited amount of agricultural land,” he says. “The entire textile industry needs to move forward based on the availability of materials, demand, and being able to do things in new and better ways. Polyester has challenges, as mentioned, which we’re meeting by using recycled material, but it also presents opportunities. It can be treated in different ways – a bit like curling ribbon when wrapping a gift – to make it more like natural materials such as linen and wool.”
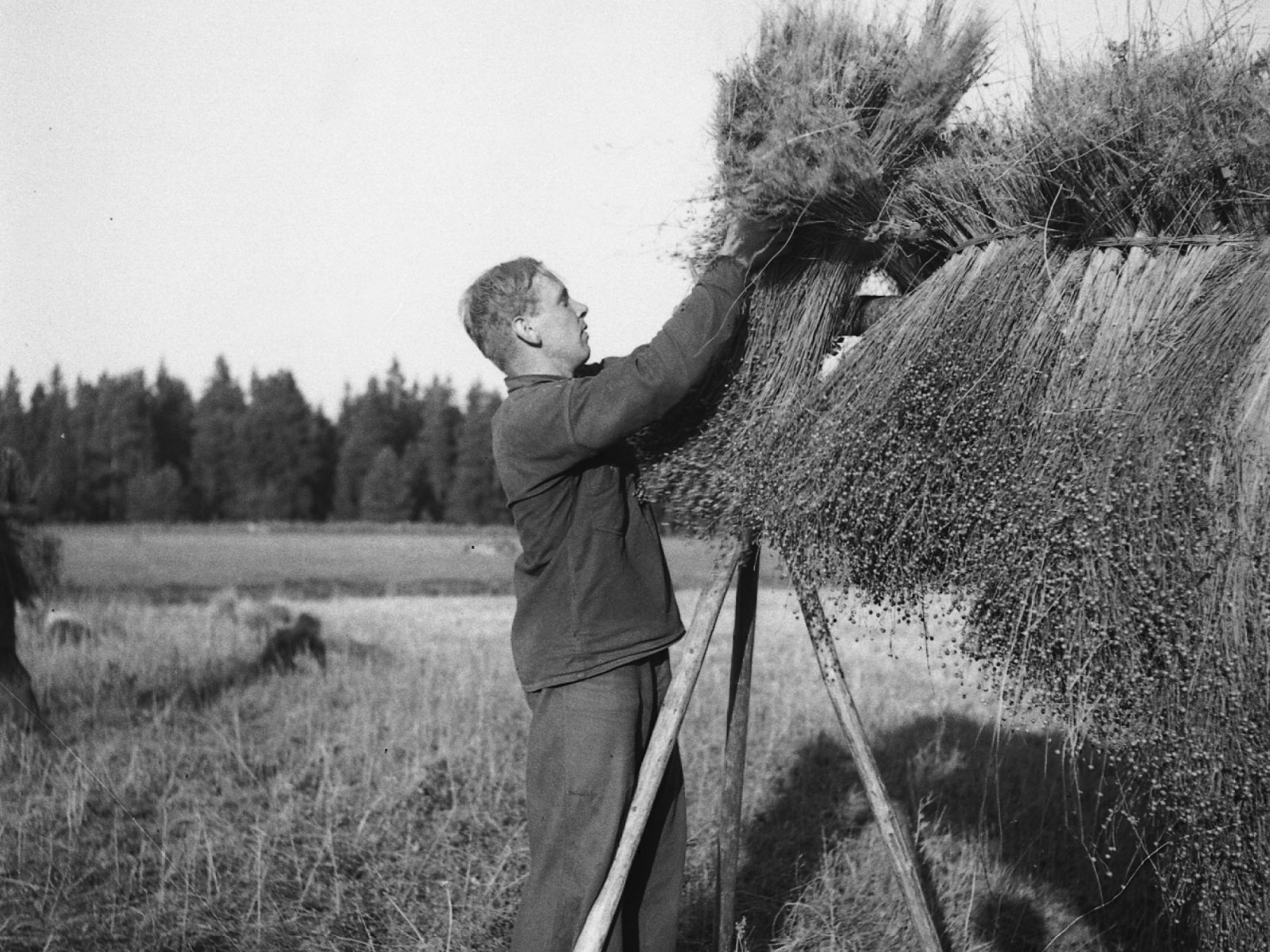
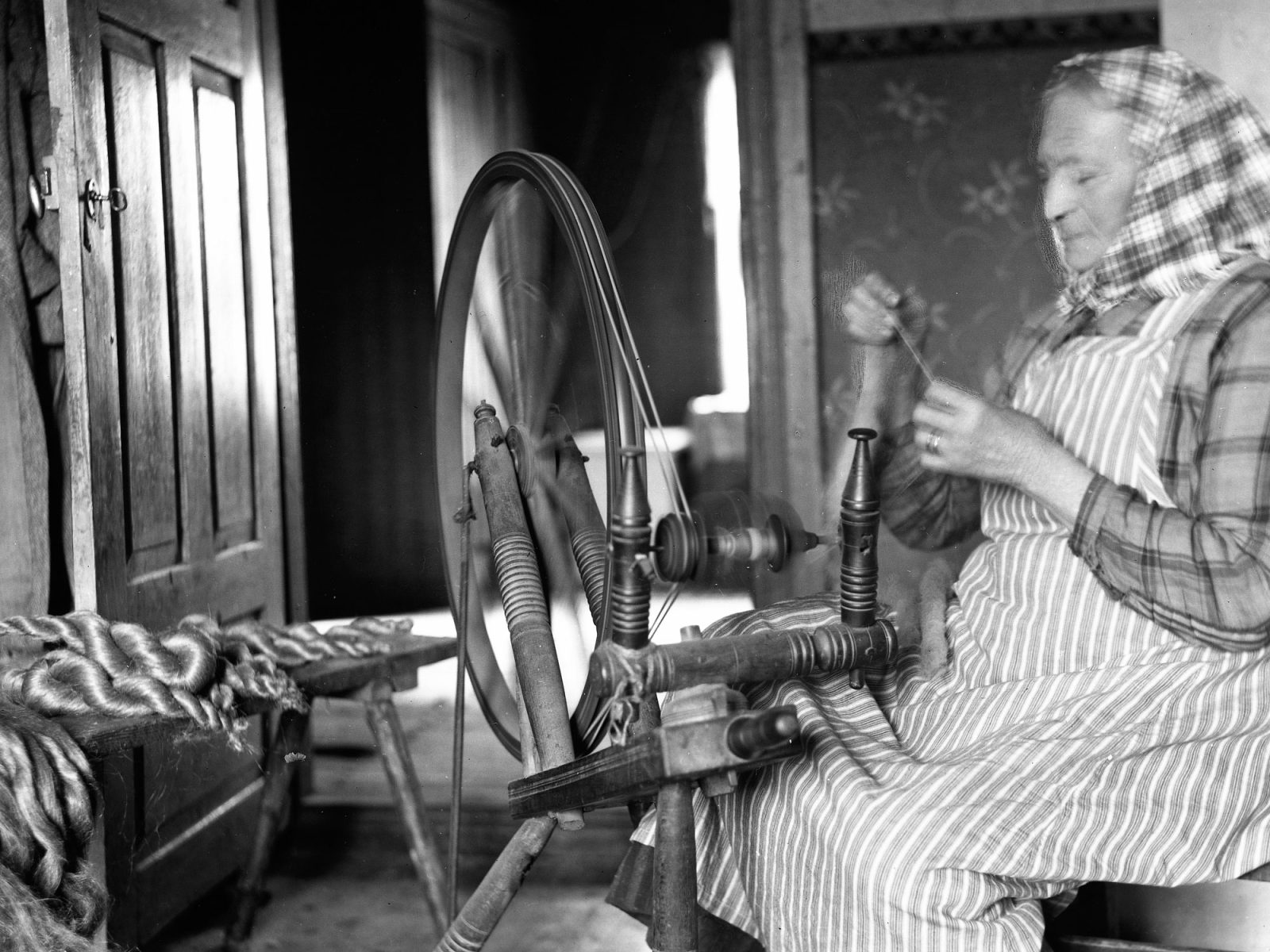
The old cultivated plant flax – the basis for linen fabric – is an example of a fibre that requires long, costly processes after harvesting, from drying, rippling and retting, to breaking, scutching and heckling. “These are ancient skills that the entire industry is now trying to find new ways to handle. Linen is part of our Scandinavian identity, but we can achieve a similar feel with textile made from hemp and jute,” says Nils Månsson.
From tree to textile
After ten years of development, textile is now being produced in a new way next to the pulp and paper mill in Nymölla, in the southern province of Skåne. The project is called ‘TreeToTextile’ and is being run by IKEA, H&M, Stora Enso and others. The aim is to develop textile fibres from wood, and which meet the requirements of low environmental impact at a low cost. The new technique will be tested and fine-tuned in Nymölla, to then be scaled up to industrial level.
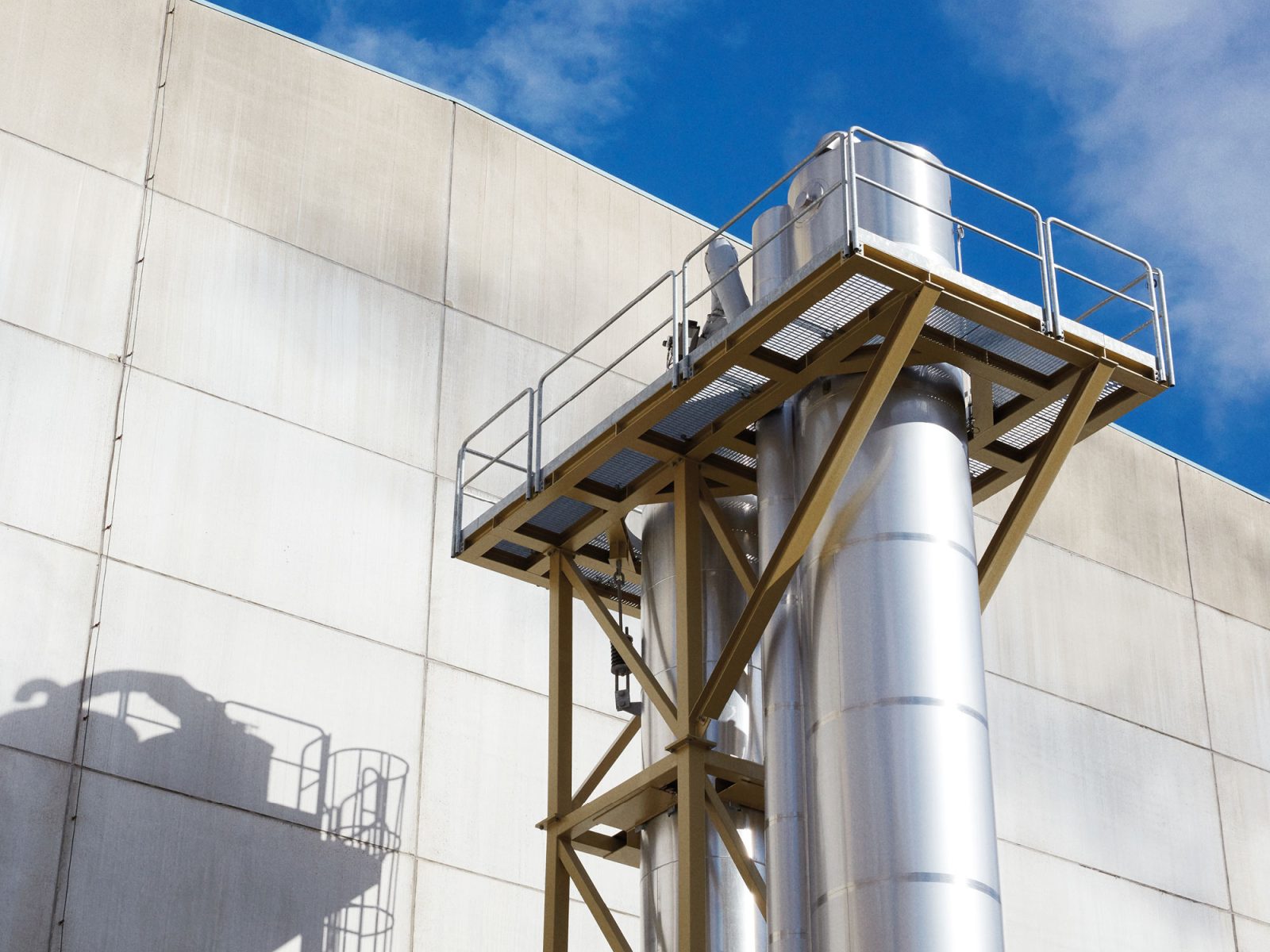
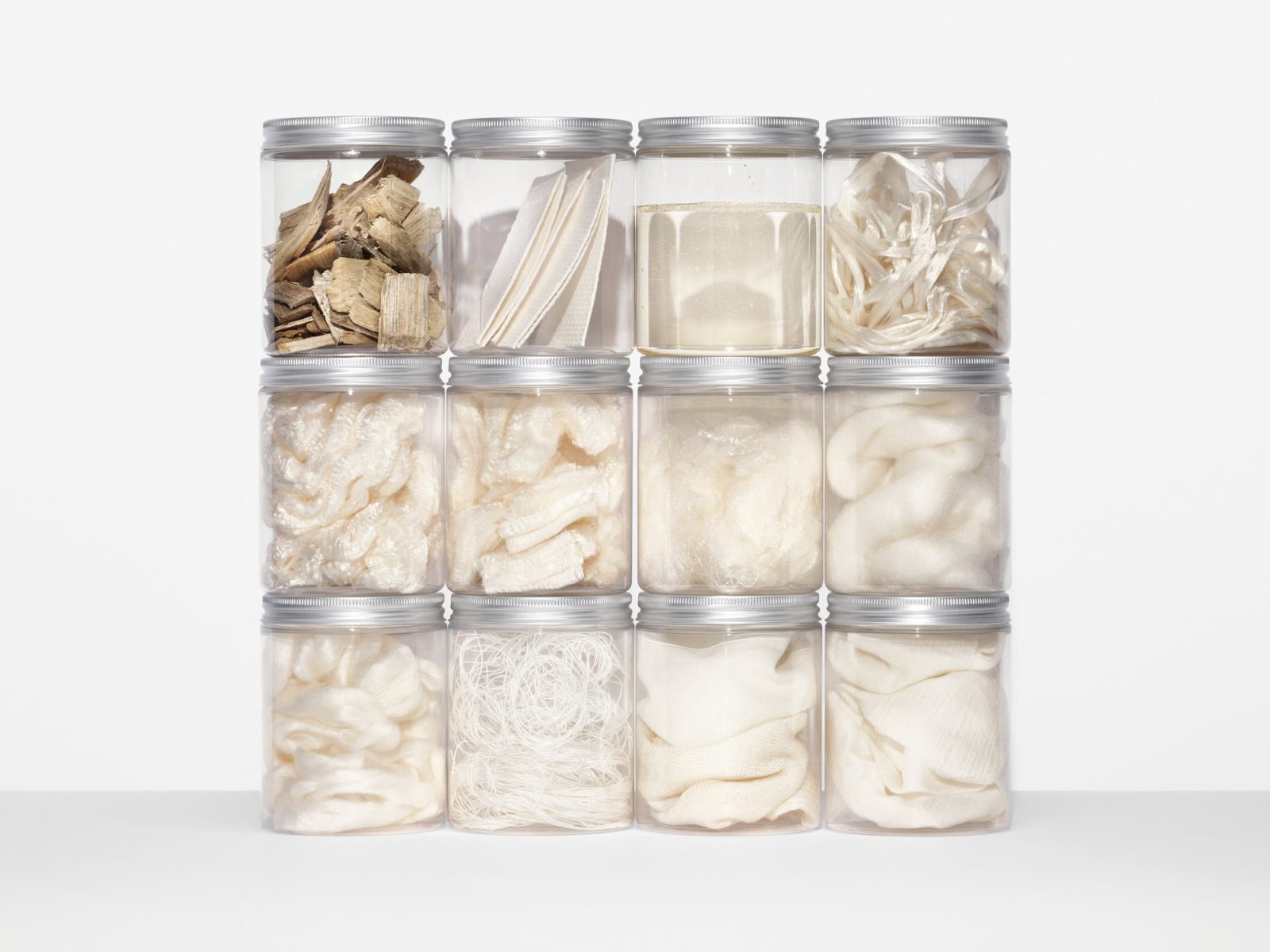
Making textile from wood is not a new idea, but existing processes for making, for example, viscose from wood pulp, can have serious negative impact on the environment if not managed correctly. A breakthrough was made in 2010, when civil engineer Lars Stigsson presented his ideas for a more sustainable process for making textile fibres from hardwood and softwood trees. He wanted to remove the toxic chemical, carbon disulphide, which dissolved the wood pulp, and also to develop technology to be able to recycle all the other chemicals.
“Development began in the lab, and a demo plant was then built where the technology could be tested on a technical and economic basis,” says Nils Månsson. “Still on a much smaller scale than anything else we make for IKEA. We’re talking about thousands of tonnes rather than hundreds of thousands.”
Unfortunately, Lars Stigsson passed away just before the TreeToTextile plant in Nymölla got up and running. But it is here that his ideas will now become reality, in the shape of a new kind of wood-based textile with a viscose-like feel, and with lower environmental impact than cotton and oil-based materials.
“From producer to consumer and back via recycling and reuse.”
Broader is better
“The reason that we at IKEA believe we can drive change is that we work so broadly,” Nils Månsson explains. “From producer to consumer and back via recycling and reuse. In textiles, there are always a lot of stages – whether a fibre is being produced or recycled. Like cotton, which has to be picked and spun, transported and dyed before IKEA can use it for a product, like a bed sheet. And then of course, we hope people will love it for many years to come. Our presence in the textile chain is a strength that enables us to influence the textile industry of the future.”